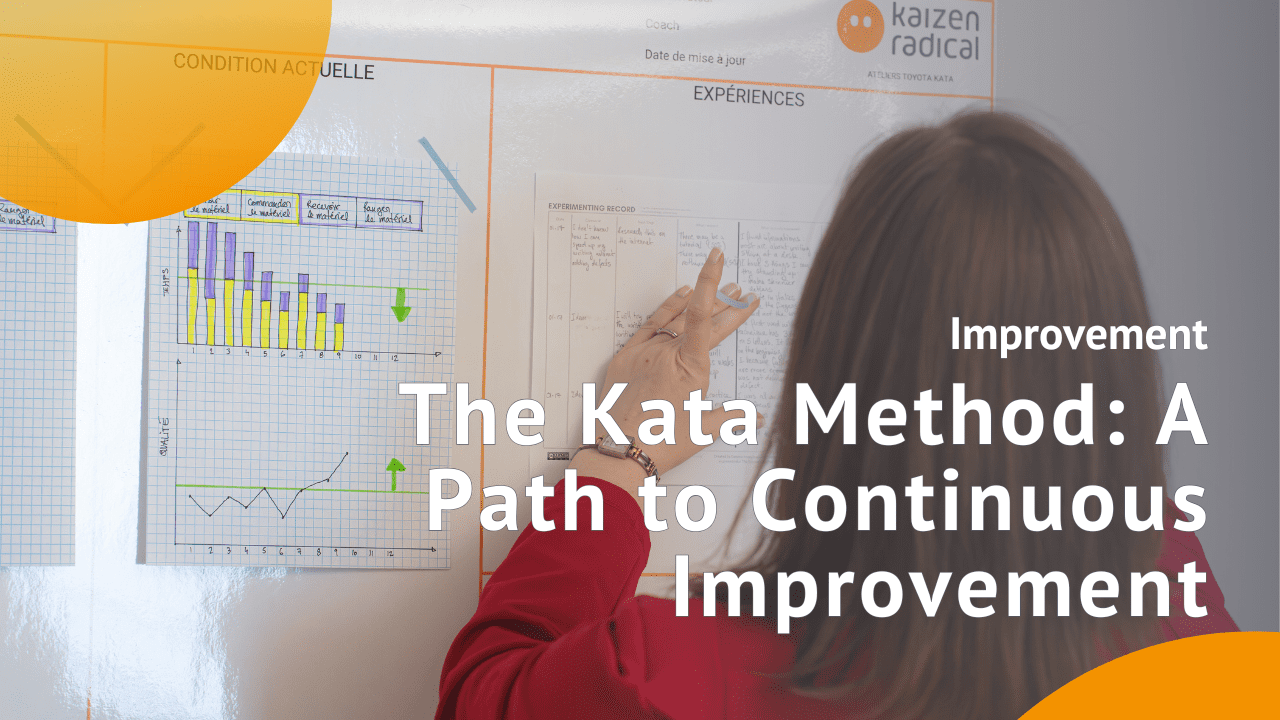
Reading time: 11 minutes
Have you ever wondered why goalkeepers save so few penalty shots in soccer? The answer is simple! Their choice to go left or right is based on… intuition. That’s right! Because the ball is coming at them so fast, it’s impossible for them to analyze its trajectory. So they make their decisions on the spur of the moment.
Not the best strategy, is it?
Yet this is what managers are all too often forced to do: navigate in a context of uncertainty and make optimal decisions without having all the information at hand. The result? Projects pile up and are managed blindly by employees in a constant state of emergency.
No time to stop and think about the meaning of our actions. So we cross our fingers and hope very much that we’re heading in the right direction to help our team win.
What if I told you that things can change? That organizations no longer have to be satisfied with these counterproductive ways of doing things? Using the KATA method, it’s possible to do things better and in the long term. All you have to do is adapt the way you work to tackle challenges differently.
In this article:
What is the kata method?
The kata method, also known as “Toyota Kata”, is a set of routines and habits that have enabled the Japanese company to become a world leader in the automotive industry.
Its foundations are based on the principle that, like the athlete or virtuoso, it is through practice that the desired excellence is achieved.
The reflexes and habits acquired through repetition help employees to develop their skills and adapt more easily to change. At the same time, they are more proactive in solving the problems they face.
Basically, they’re encouraged to adopt an approach based on continuous learning and improvement… one step at a time.
Here are the basic principles of katas:
Focus on process rather than results
Rather than focusing on the end result, the KATA method emphasizes the improvement process itself. The aim is to develop routines and habits that will ultimately enable the organization to achieve the desired objective in a sustainable way.
Learning and experimentation
The KATA method encourages experimentation. Employees are encouraged to try out new ideas, learn from their mistakes and adapt continuously.
Coaching and support
Managers play an essential role in implementing the KATA method. They adopt a coaching posture to guide and support their teams throughout the process.
Problem solving
The KATA method provides teams with a structured framework and precise tools and techniques to identify and solve problems systematically.
Target orientation
Each improvement initiative is structured around a goal or challenge to be achieved. This way, everyone stays on course, following a clear and precise direction.
Respect for people
The KATA method puts employees at the heart of the improvement process. It values their skills, creativity and commitment.
Improvement kata in practice – the 4 steps to follow
The Kata method is a fixed routine that we repeat for each experiment or project. The 4 steps are simple, but require rigor and discipline.
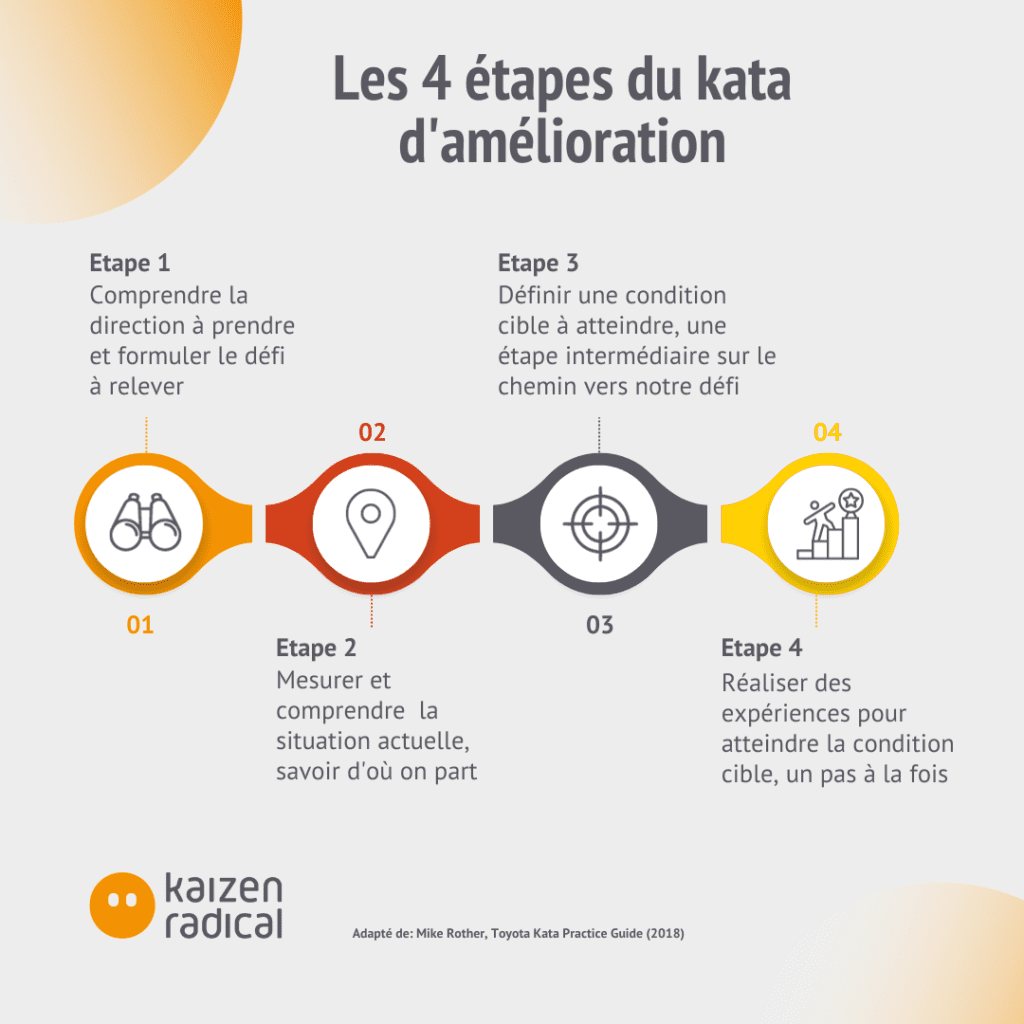
Step 1: Understanding the vision or challenge
Before taking action, it’s important to clearly define the result you want to achieve. This ensures that everyone keeps their eyes on the same goal.
Example: Choosing the destination for your next trip.
Step 2: Understanding the current condition
Once the challenge is well defined and understood, it’s time to analyze the current state of affairs. The process is studied and measured to identify the gaps between reality (where we’re starting from, what’s happening now) and vision (where we’re going, what should happen once we’ve reached our goal). In this way, we can determine the scale of the task ahead.
Example: Know the starting point of your next trip
Step 3: Define the following target condition
When we use the KATA method, we don’t immediately define all the actions that will lead us to the expected result. Instead, they are established gradually, as we advance one step at a time towards thenext objective. In this way, we retain the flexibility to test as many solutions as necessary to achieve the goal.
Example: Planning the next stage in the journey to your destination (refuelling, lunch break, hotel)
Step 4: Experiment to overcome obstacles
This final stage is divided into two parts. First, we identify the immediate obstacles. That is, everything that will prevent us from achieving the target condition defined in the previous step. Then, we test different approaches and solutions to overcome these obstacles.
Example: Adapt the route to your destination according to obstacles (weather, roadworks, traffic, accidents, etc.).
Advantages of the kata method
The most obvious benefit of the kata method is, of course, the achievement of corporate business objectives. But there are others:
Improving efficiency
By concentrating on small, regular improvements, efficiency is multiplied and the results obtained are of the highest quality.
Problem solving and prevention
By constantly identifying and adjusting inefficiencies in their processes, companies prevent “problems” from getting too big.
Adaptability
The kata method helps companies adapt more easily to change. By practicing continuous improvement, teams become more flexible and better prepared to face new situations and unexpected challenges.
Employee commitment
It’s a well-known fact that employees are more committed when they are actively involved in improving their work. Since the kata method involves everyone playing a part in the process, motivation and job satisfaction are inevitably increased.
Communication and collaboration
By involving everyone in the improvement process, the kata method encourages greater collaboration and clearer communication between employees. Team spirit is also strengthened by combining everyone’s strengths. Everyone works in synergy to achieve a common goal.
Skills development
Since employees are engaged in a continuous, structured learning process, they increase their skills and autonomy. At the same time, they become more adept at systematically solvingcomplex problems.
Learning culture
By fostering a culture of continuous learning, the kata method enriches the knowledge pool of the entire organization. Indeed, as employees are encouraged to learn from their experiences – rather than being reprimanded for their “mistakes” – they are more inclined to share them with their colleagues.
Culture of continuous improvement
The kata method facilitates the creation of a culture of continuous improvement, where the achievement of excellence is driven by the contribution of every member of the organization. By promoting innovation and resilience, teams can adapt more quickly to market changes.
The role of scientific thinking in kata
The kata method is unsurprisingly based on the use of scientific thinking. And the main tool it needs to be effective is none other than the brain.
This precious organ operates in 2 modes:
- System 1 or automatic, which is fast, instinctive and emotional.
This is the system that, for example, is at the controls when driving a car. It kicks in to make sure you check your rear-view mirror and blind spot when you change lanes. In fact, it’s an automatic sequence that experience allows you to perform without even thinking about it. As it requires very little energy, this is the system that is active by default. - System 2, or algorithmic, is slow, thoughtful and logical.
It’s the one that takes over when it’s time to solve a complex problem or make an important choice. It also kicks in when we learn a new skill. In other words, BEFORE it is automated. This is the case of the learner driver, for example.
More concretely, in the kata method, system 2 is used first… with the aim of replacing system 1.
There are 2 strategies for developing scientific thinking:
- Adopt the habit of slowing down to think before making a decision or proposing a solution.
- Set up a routine to automate a logical thinking pattern which, over time, will become natural and replace our tendency to jump to conclusions.
In short, even if it’s primarily scientific thinking that’s called upon in the practice of kata, once properly established and integrated, the routine becomes a reflex. A new, instinctive way of thinking.
It transforms the way we work, the way we approach challenges, and prevents teams from moving forward blindly.
No more improvisation for managers! Never again will they throw themselves randomly into the soccer net.
Because, unlike goalkeepers taking penalty kicks, they will have learned to assess the movement and progress of the ball step by step.
To find out more about Katas, whatever your level, discover the options available in our training catalog.
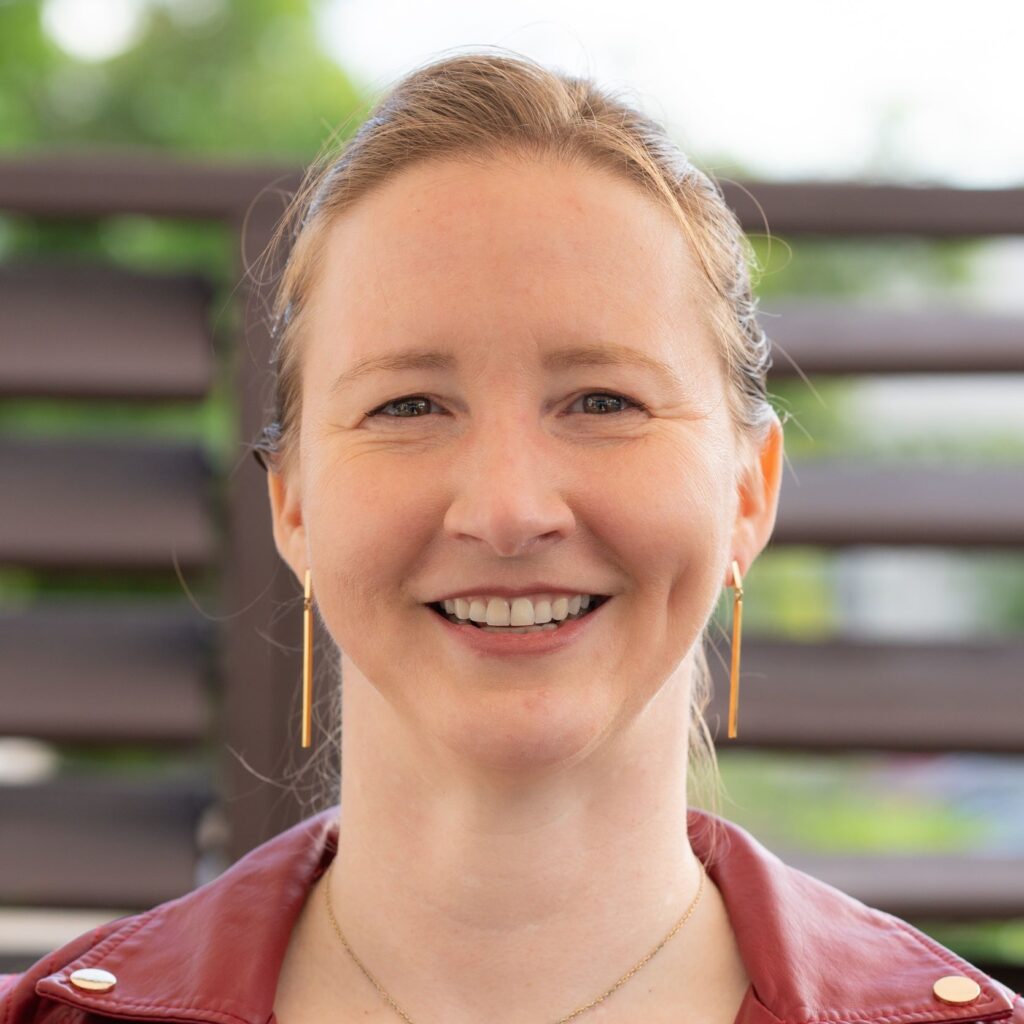
By Julie Savage-Fournier
Industrial engineer
Lean Six Sigma Master Black Belt
Bonus questions
The kata method is a structured approach to continuous improvement based on scientific thinking. It involves achieving objectives by applying a cycle of planning, verification and action to refine and perfect processes.
The kata method is distinguished by its iterative and scientific nature, encouraging continuous testing and adjustment of procedures until they reach optimum performance, rather than simply relying on quick correction of the symptoms of a problem.
It is also a series of learning routines to be practiced in order to deploy a culture of continuous improvement throughout the company, rather than applying one-off corrective actions.
The kata method is relevant to any organization or team seeking to improve its processes, increase efficiency and foster a culture of continuous improvement. It is particularly useful for industries that require a high degree of adaptability and responsiveness. It is the method of choice for industries and business areas faced with volatility and uncertainty.
By promoting a culture of innovation and continuous improvement, the kata method improves not only productivity but also employee satisfaction, which ultimately boosts the organization’s efficiency and competitiveness.
Although initial training to understand its basic principles and implementation is recommended, the kata approach is designed to be intuitive and scalable. Teams can quickly adopt the method and build on their learning for success. A one-day introductory training course can be enough to get the ball rolling! To make sure you master all the concepts, Camp Kata is for you…